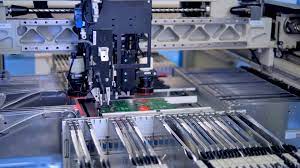
To create multi-layered pcb assemblers, multiple cores are stacked together and bonded, creating a sandwich-like structure. These layers are connected through small holes called vias, which are drilled or laser-drilled to establish electrical connections between the different layers. The vias are then plated with copper to ensure a solid connection.
After the circuit pattern is created and all layers are connected, the next step in PCB fabrication is to apply a solder mask. This is a protective layer that covers the copper traces and vias, preventing unintended electrical connections and providing a surface for soldering components in the assembly stage. Silk-screen printing is used to add labels and symbols for component placement on the PCB.
The final step in PCB fabrication is the application of a surface finish, which protects the exposed copper from oxidation and ensures a reliable electrical connection. Common surface finishes include lead-free solder, gold plating, and organic surface protectants. Each has its advantages, depending on the specific application.
In conclusion, PCB fabrication is a highly precise and intricate process that is essential for the functioning of virtually all electronic devices. As technology continues to advance, PCBs become smaller, denser, and more complex, requiring even greater precision and expertise in their fabrication. The ongoing development of new materials, processes, and techniques in PCB fabrication ensures that these unsung heroes of the tech world will continue to enable the devices and innovations that shape our lives.